立式注塑机的电能消耗主要表现在以下几个部分:液压系统油泵的电能消耗;加热器的电能消耗;循环冷却水泵的电能消耗。立式注塑机的节能技术,实际上主要包涵三个方面:一是节能注射成型技术,二是节能的执行机构,三是节能的动力驱动系统。立式注塑机最主要的能耗即是动力驱动系统,立式注塑机节能的重点即是提高动力驱动系统本身的能耗效率及驱动系统输出功率与执行机构执行功率达到自适应调节匹配,两者之间的能量利用率越高,即系统节能率越高,达到节省能源的功效。节能动力驱动系统是立式注塑机节能的主要研发课题
。
1 立式注塑机动力驱动系统分析
动力驱动系统一般有以下三种:液压驱动系统、全电子驱动系统和液电混合驱动系统。液压驱动系统是立式注塑机泛使用的动力驱动系统,是节能动力驱动系统重点研究对象。从节能角度来说,全电子驱动系统和电液混合驱动系统是对液压驱动系统能量利用率不高的创新发展,是两种理想的节能驱动系统。长期以来,立式注塑机节能液压系统是重点研究的节能动力驱动系统。
目前立式注塑机供油泵的驱动主要有三种方式:普通电机加变量泵、变频电机加定量泵和变频电机加变量泵。变转速控制的效率比变排量控制的效率高,而用变排量和变转速复合控制的效率比变转速控制的效率高。变转速控制的响应比变排量的响应快。尽管异步电机的控制技术也日渐完善,但其自身的功率因数、效率以及发热问题始终无法克服。同步电机技术越来越成熟,制造成本上也与异步电机越来越接近,正在越来越多的场合取代异步电机。同步电机在立式注塑机上的应用将成为趋势。
2 立式注塑机控制系统分析
立式注塑机控制系统=驱动系统+电子控制器,立式注塑机的驱动系统根据其控制的形式可以分为三类,即液压控制式、电动控制式与电动/液压复合控制。
2.1 采用泵供油复合控制阀调节的控制系统
采用定量泵供油,通过流量/压力复合控制阀调节式的缺点在于以下几点:第一是控制精度不高。整个控制其实是一个开关控制,由于开关阀的启闭有数十到数百毫秒的延时,所以对注射位置、开合模位置的控制精度不高,并且使运动速度难以提高。第二是能源耗费大。采用P/Q阀后,虽然压力可以随着工艺过程的不同而改变,但是定量泵所输出的流量一定,而不同的工艺流程需要的流量不同,多余的流量就通过溢流阀,造成了很大的溢流损失,特别是在高压、小流量的保压过程时损耗更大。同时,依靠流量阀的节流来获得不同的流量,其节流损失也相当大。溢流损失及节流损失最终都体现在液压油的发热上,而立式注塑机液压系统由于空间所限,油箱体积不能很大,必须配置油液的冷却系统来保证液压系统的正常工作。第三是噪声大。高速运行的大功率电动机与液压泵噪声很大,使得工作环境恶劣。
采用变量泵节能型液压控制系统。在立式注塑机液压控制系统中,其能量损失是由节流损失与溢流损失两大部分组成的,节能的关键就在于减少这两类的损失。采用变量泵是一个很好的办法。它通过调节泵的排量,从而使泵输出的流量、压力与系统的要求相适应,最大限度地减少液压系统的溢流损失与节流损失,可以显著节能。采用比例变量泵系统的全液压式立式注塑机是目前国内立式注塑机生产厂家的主流产品,技术比较成熟。采用变量泵的缺点在于变量泵价格昂贵、结构复杂、调试维护不易和易受油液污染的影响。若采用比例/伺服变量泵,价格要比定量泵贵得多,而且较易受到油液污染的影响。
2.2 采用电液伺服阀控制的控制系统
高速液压控制系统对于一些需要快速运动的回路,如开合模、注射回路,采用电液伺服阀代替开关阀,利用电液伺服阀的快速响应能力实现对运动的高速、精确控制,可以对立式注塑机的流量与压力形成闭环控制,获得对位置的精确控制。它的缺点在于价格昂贵与抗油污能力差,这也是由于电液伺服阀本身的特点所决定的。大流量的电液伺服阀及其放大器均较昂贵,并且对液压油的污染非常敏感,而立式注塑机的工作场合一般均较为恶劣,如果不能对液压油的污染进行控制,极易发生阀卡的故障。
2.3 变频器节能型液压控制系统
目前变频液压立式注塑机的动力源主要有两种变频驱动方式:一种为普通异步电动机通过变频调速与定量泵组成动力源;另一种为用高响应的交流(AC)伺服电动机驱动定量泵作为动力源。当采用AC伺服电动机驱动定量泵作为动力源时,电动机成本较高,但AC伺服电动机响应速度快、过载能力高,压力和流量均可通过改变电动机转速来进行闭环控制,适合于动态响应要求高的场合。
采用变频器控制普通的三相异步电动机,从而驱动定量液压泵,通过变频器改变电动机的转速,达到改变液压泵输出流量的目的。在国内,变频液压技术主要用于对原有立式注塑机液压系统进行改造。立式注塑机变频调速存在的问题:立式注塑机液压系统必须严格按照注塑工艺要求提供所需的流量和压力,并应具有较高的重复精度和灵敏度,否则将对制品的质量有极大的影响。从目前国内外在立式注塑机上应用变频液压技术的研究结果看,尚存在诸如低速特性差,动态响应慢,调速精度不易保证等问题。
2.3.1 低速稳定性
在 立式注塑机液压系统中,如果液压泵的转速过低,自吸能力下降,容易造成吸没不充分而形成气蚀,引起噪声和流量脉动,影响速度的稳定性。二是低速过载能力差,特别是电动机制动时速度慢,不能很好满足控制系统的要求。因此,油泵存在一个最低稳定转速限制问题,使得变频液压系统在小流量的状态下节能效果并不理想。另外,低频力矩不足和异步电动机低频运行时固有的不稳定性,电动机转动部分与逆变器直流中间环节中滤波,贮能元件之间能量交换中产生的谐振现象,无功功率的影响等都是引起转速不稳定的可能原因解决低速稳定性,可以从选择低速性能好的泵和高性能变频器或伺服控制器来考虑,但需要付出较高的成本,可以采用合理的控制结构和好的控制算法,通过软件补偿的办法来优化系统参数,提高系统的动态品质和低速稳定性,使变频液压系统满足注塑工艺过程,达到预期的节能和系统优化效果。
2.3.2 响应快速性
从立式注塑机的特点和注塑的工艺过程来看,需要系统的响应快,否则会影响注塑制品的质量和生产效率,因此响应的快速性是立式注塑机驱动控制系统的一个重要的性能指标之一。
变频容积液压控制系统是通过改变电动机转速来改变液压系统的流量。由于一般的异步电动机的转动惯量大于液压泵的转动惯量以及由于变频器的过载能力有限,影响了加速性能。因此一般变频容积控制系统比传统容积控制系统的响应要慢。在立式注塑机变频液压驱动系统中选择性能好的变频器可以提高立式注塑机驱动控制系统响应的快速性。在矢量型变频器中,通过设定速度调节器的比例增益P和积分时间I,可以改变矢量控制的速度响应特性,这个速度响应特性直接影响到立式注塑机成型周期的快慢和执行动作的力度.其调节的方法是既要加快响应特性,同时避免产生电动机振荡。另外采用高响应的交流伺服电动机代替一般的异步电动机,可以很大地提高响应速度,可使用在动态响应高的注塑生产场合。当既要求大范围调速,又要求响应速度较快时,可采用综合调速控制。既充分利用变转速容积控制系统调速范围大,节能效果显著的特点,又保留阀控缸或阀控马达响应快的优点,组成复合调速系统变频系统交流电动机速度在变频器的控制下随负载变化而变化,受磁滞效应及转动惯量的影响,响应速度慢(800~1000ms)。
2.3.3 控制精度
影响调速精度的一个主要原因是速度刚度。所谓速度刚度是指执行器的速度不随负载变化的能力;另一个主要原因是系统的慢时变特性,如液压系统中的油液温度、油液黏性和泄漏量的大小等都会随着时间呈非线性变化,从而影响系统的输出特性,影响调速精度。为消除或减弱负载对转速的影响以及液压系统的慢时变特性对系统输出的影响,需要从两个方面来考虑,一个方面是要确保电动机转速不随负载变化而变化,另一个方面是要消除或减小液压系统的慢时变特性对系统输出的影响,对变频器设定合适的转矩补偿和滑差补偿,在负载变化时适当调节泵的(电动机的)转速,即可适度补偿回路泄漏的流量,维持执行器转速的稳定性,保证其速度刚度得以较大提高,符合注塑工艺过程和注塑产品所需要的控制精度。
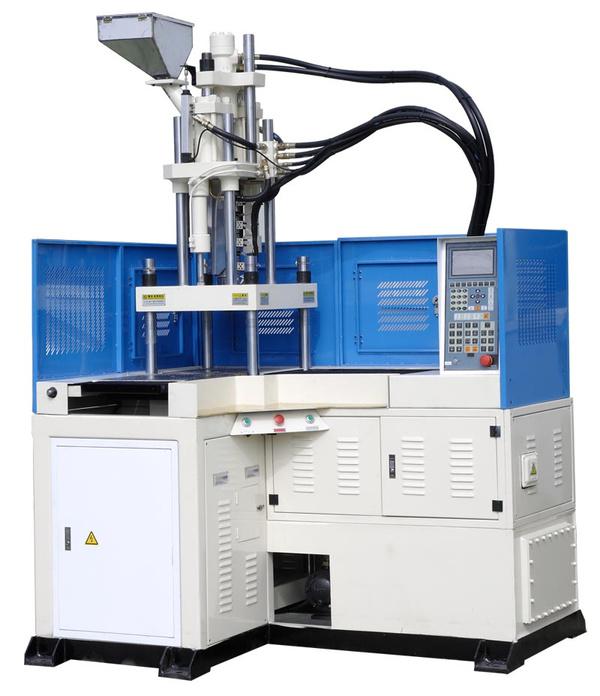
2.4 全电动控制系统
由于伺服电动机在功率及响应方面均有较大的提高,且伺服控制器的功率及控制精度也有提高,即出现了驱动部分采用伺服电动机加滚珠丝杆传动方式的全电动控制式立式注塑机。它特别适用于小型的高速精密立式注塑机。据统计,目前北美立式注塑机市场中有25%为全电动立式注塑机。全电动立式注塑机将成为注射机市场的主流。电动控制式的优点有四方面。第一是节能。全电动控制式为目前最为节能的驱动方式。它的电力消耗仅为液压式的1/3左右,而且越是大型机,节能越明显。第二是无污染。由于不使用液压油,电动式立式注塑机不需要冷却液压油的设备,节省了资源,无漏油、漏水现象,可以保持工作场地的清洁。第三是易于控制。电动控制系统的可控性好,所以稳定性高,控制精度高。第四是成型周期短。与液压式系统不同,它有多个驱动电动机,从而使各动作相对独立,可以实现部分动作的复合动作,缩短成型周期。缺点有:第一是价格昂贵。由于伺服电动机及其驱动器价格昂贵,目前全电动式的要比液压式的价格高约2~3成。第二是对环境要求高。全电动式立式注塑机要求环境清洁,以保证其控制电路、电动机等的正常运转。第三是构成大型立式注塑机较困难。由于缺乏经济的大型伺服电动机,全电动立式注塑机的大型化受到限制。第四是受机械传动部件的限制。由于传动部分为机械传动,磨损问题较为突出,整机后期维修费用相对较高。
2.5 电动/液压复合控制式
电动液压复合控制式的优点在于融合了全电动与全液压式两者的优点,即可以利用液压系统功率大的优点,又可以利用电动系统节能、快速的特点。同时由于采用了多个驱动器,也可以实现部分动作的复合动作,缩短成型周期。缺点在于结构较复杂,控制困难,要协调电动与液压两个不同系统的工作。电动-液压式立式注塑机是集液压和电驱动于一体的新型立式注塑机,它融合了全液压式立式注塑机的高性能和全电动式的节能优点,这种电动-液压相结合的复合式立式注塑机已成为立式注塑机技术发展方向。
3 国内外发展情况及未来展望
应用变量泵与比例阀构成的负载感应系统,是电液控制中最基本的节能方法,已在国外的工程机械中被广泛应用,不足的是仍存在与流量有关的能量损失;p/Q复合泵与变频调速电机驱动的定量泵均不存在任何节流量损失。相比之下,应用调频电机加定量泵可进一步减少空转能耗及噪声,更具竞争性,但应进一步提高其动态快速性。
伺服电机驱动系统,由于伺服电机使用永久磁铁结构,且由于转矩及惯量的密切配合下,又在低惯量的转子的配合下,免除了脉动转矩,在速度范围内有着良好的加减速度动态反应特性。因转矩是由感应式电流产生,具有完满磁性分布之高密度磁通所生,在2000r/min速度范围内,输出高比例(可达到218倍)的额定转矩情况下,能保持非常低的转矩波动,在非常低的速度下也可有大的定转矩区,达到衡定的流量输出。转速随系统流量需求而改变,反应速度比伺服阀快01004s,液压系统基本上不需冷却水,对于保压及冷却时间长的制品,节能可达80%。交流伺服电机的最高转速可达4000r/min,从理论上讲,与之相配的液压泵的排量可根据最高转速选择,选用比一般系统中应用的更小排量的液压泵,降低系统中应用液压泵的成本。但目前一般液压泵的最高转速为1800r/min,同时,考虑到液压泵的高速工作噪音及使用寿命,选用液压泵的工作转速低于1800r/min、较大排量的液压泵与伺服电机组成动力驱动系统,所以还不能充分发挥交流伺服电机能高速运转的优良特性,提高了驱动系统的成本。高响应的交流伺服电机驱动定量泵系统在立式注塑机上的推广应用,有待于高速低噪音液压泵的研发,以降低制造成本。如单纯从节能角度来推广应用高响应的交流伺服电机驱动定量泵系统,由于成本太高,达不到效果。如把高响应的交流伺服电机驱动定量泵系统,应用于普通立式注塑机上,仅体现出节能效果,只能当展品,不能成为商品。应把伺服电机高速灵敏反应的特性与精密注射成型结合起来,创新出一种新的高性能的注射成型,能对高端的塑料制品进行特定加工,才能使之应用越来越广。特别对电子类薄壁产品注射成型,更显示出高性能高精度注射成型的优势。
变量泵和电液比例阀结合的负载敏感泵节能控制系统,整个控制机构由差压控制型径向变量柱塞泵、含位置闭环的高速比例阀、以及压力传感器和位移传感器组成,提高了动态响应速度。控制流量由比例阀与检测变量泵偏心量的位移传感器构成的位置闭环系统完成。通过压力传感器补偿因泄漏造成的流量损失,使泵输出的流量在0~10V内与设定值信号成线性比例。控制系统压力由比例阀与压力传感器构成的电闭环回路完成,压力与流量两种控制状态的分离与转换由电子放大器根据设定信号自动完成。系统的输出流量由0增大到90%时,响应时间约为50ms;而由90%输出流量减小为0时,响应时间约为30ms,系统压力的动态响应时间当负载容腔为4L时,小于200ms,均与高性能的比例阀相当,因而完全适合于立式注塑机的过程控制。负载敏感比例泵节能液压系统,液压动力输出随负载而同步化,其差值达到最小,基本上没有能量浪费,与定量系统相比,节能达到30%~60%,是理想的节能液压系统。
全电动驱动系统,由于各个执行机构都有独立的伺服电机驱动,能进行复合动作,电动立式注塑机市场迅速发展,国内制造商目前仍只能提供样机,开发出的全电动驱动系统立式注塑机,注射成型的技术性能低国际上几个挡次,体现不出全电动驱动系统立式注塑机的高性能的综合技术优势。全电动立式注塑机在国内的研究开发起步较晚,伺服电机、专用控制器等核心技术还没掌握,整体技术上与日本等先进国家相比还存在着较大的差距。技术与成本将是中国制造商开发全电动机面对的最大问题。然而,即便克服了技术瓶颈,成功开发出电动式立式注塑机,成本高昂问题仍将困扰着欧美日以外的电动式立式注塑机制造商。因为与欧美日相近甚至更高的零件成本、加上没有特色的控制系统,难以说服客户采用国内制造的电动式立式注塑机。
因此,在电价节节扬升、企业要求压缩成本的情况下,节能环保型立式注塑机代表了塑机发展方向,谁先走一步,谁必定抢得市场先机。正是看到这一点,越来越多的生产企业将产品节能研发置于重要位置。
尽管我国 立式注塑机企业已经具备了研发节能立式注塑机的实力,但从用户反映的情况来看,目前国内节能立式注塑机在质量、技术方面仍参差不齐,尤其是高端节能型立式注塑机市场还是国外产品占主流。节能型立式注塑机可以说是全世界塑机企业研究的重点,我国既然已经有能力自行研发,就更应该加快发展步伐。